What is the process of cutting the steel?
- Joyce Clark
- May 27, 2022
- 3 min read
Metal fabrication is a complicated process that requires the use of many different types inlayed with each other.
There are several approaches you can take for cutting your materials, but it's important to know about them before getting started so as not to make mistakes during production time!
Metal cutting has been around for centuries. From basic hand-held items like hacksaws, chisels, or shears to more sophisticated machinery there's a method that will suit your needs!

The first step is to choose the proper equipment for the job, based on factors like budget, efficiency, and overall project requirements.
There are several different types of machinery that can be used for metal cutting, including saws, lasers, plasma torches, and waterjet cutters.
Once you've determined the best tools for your project, the next step is to prepare your materials.
This usually involves marking out the desired cutting locations and creating appropriate holding fixtures if needed.
Depending on the type of material being cut and the equipment used, this may also involve pre-heating or cooling as well.
Next, the actual cutting process begins. Depending on the type of materials and tools being used, this can involve a variety of different techniques.
For example, sawing typically involves using a blade to make precise cuts through the material, while lasers and plasma torches rely on heat energy to melt or burn away at the steel.

Waterjet cutting is another popular method that involves using an abrasive water stream to slice through materials, while also preventing heat buildup and damaging the material.
Once the cutting is complete, it's important to inspect the results and make any final adjustments or clean-up as needed.
Depending on the specific project requirements, this may involve further processing of the cut parts or adding additional finishing touches.
Grinding
Grinding, welding and painting are all common post-cutting processes that can be used to enhance the functionality or appearance of the final product.
By following these steps, you can ensure that your metal cutting project is completed successfully from start to finish!
Grinding is almost always done by hand using a grinding machine, though some larger operations have finishing machines they use for the process.
There are many different types of machines used for grinding, including bench grinders, cylinder grinders, surface grinders, bit grinders, and more.
Drilling
Metal drilling can be done with rotary or fixed-contact machines. The process of applying pressure and rotation on top of the metal component creates a hole in it, which will then become part of your product's shape!
There are many different types of drill bits that can be used for metal drilling, depending on the size and shape of the hole you need to create.
Tapping
Tapping is a process where threads are cut into the inside of a hole, which allows for a screw or bolt to be inserted and screwed in place.
This is a common method for creating fasteners and joining two pieces of metal together.
There are two main types of taps: hand taps and machine taps. Hand taps are used for smaller, less precise holes, while machine taps are used for larger, more precise holes.
Both types of taps require the use of a tap handle, which is a tool that helps to apply the necessary pressure and rotation to create the threads.
Reaming
Reaming is a process where a hole is enlarged slightly, usually to ensure a tight fit for another component.
This can be done by hand using a reamer, or by machine using a CNC reamer.
There are several different factors that can affect the quality and effectiveness of the reaming process, including the material being reamed, the size of the hole, and the type of reamer used.
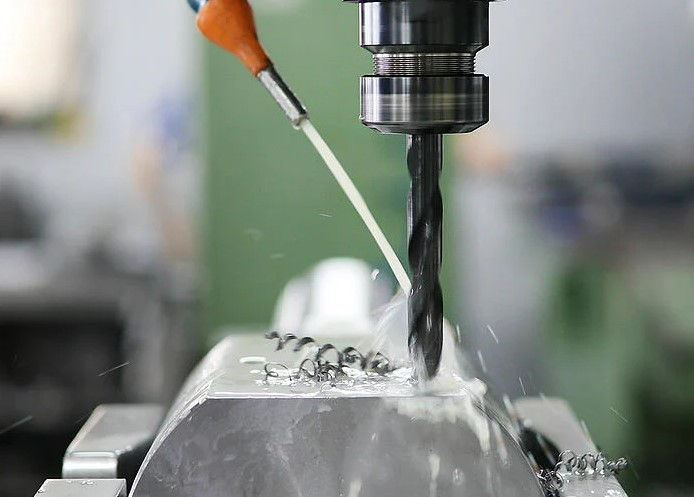
Overall, careful preparation, attention to detail, and good tooling are essential for achieving a high-quality finish when reaming. Welding is one of the most common methods for joining metal components together.
There are several different types of welding techniques and machines, including arc welding, MIG welding, TIG welding, oxy-acetylene welding, spot welding, seam welding, and more.
Regardless of which method is used, it's important to follow proper safety procedures when welding to avoid injury.
When done correctly, welding can create a strong and permanent bond between two pieces of metal. Painting is another common way to finish metal parts and components.
This can be done by hand using a paintbrush or spray paint, or by machine using an automated painting system.
There are many different types of paints that can be used, depending on the desired finish and level of protection.
Overall, careful preparation and attention to detail are key when painting metal parts or components in order to get a high-quality, long-lasting finish.
In summary, there are several different processes that are commonly used when cutting steel and other metals.
Each process has its own set of benefits and drawbacks, so it's important to choose the one that is best suited for your specific project requirements.
Comments